
Simply investigating the lighting could take time and resources away from the investigation so the first step would be to see if a part is installed.Ĭauses of a part not being installed can be listed as sub-branches, but the priority should be on determining if the part was installed or not. Therefore, the part not properly installed would be listed in the Ishikawa diagram. In this example, lighting could cause an employee to make a mistake resulting in a part not properly installed. Instead, the result of bad lighting should be listed and then empirically investigated. For example, “lighting” is a typical example under “environment” however, it is seldom clear how lighting could lead to the failure. A good problem statement would be: “Customer X reports 2 shafts with part numbers 54635v4 found in customer’s assembly department with length 14.5 +/-2 mm measuring 14.12 mm and 14.11 mm.”Įlements in the Ishikawa diagram should be able to explain how the failure happened. For example, a problem statement may start as, “ Customer X reports Product A does not work.” The rest of the problem statement would then clarify what “does not work” means in technical terms based upon the available data or evidence. The customer’s description does not need to be correct it should reflect the customer’s words and be clear that it is a quote and not an observation. The customer’s description of the failure.
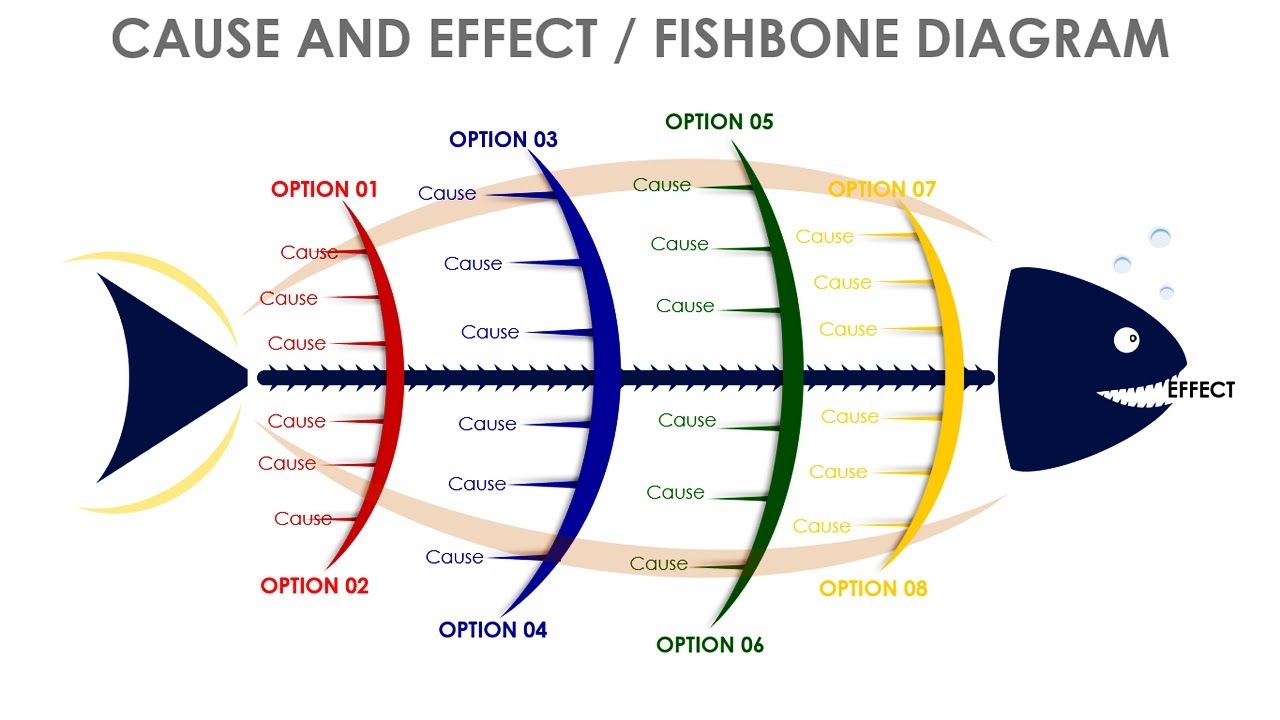
The problem statement should include all of the factual details available at the start of the investigation including:
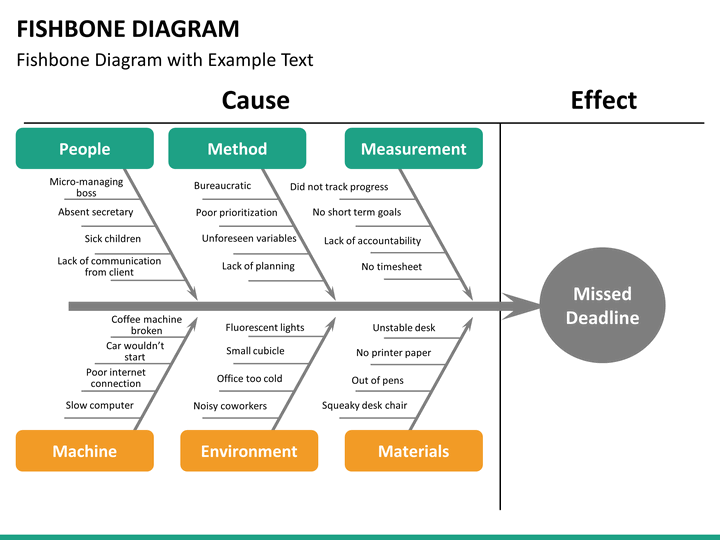
Although critical for starting an RCA, the problem statement is often overlooked, too simple or not well thought out. Once a problem-solving team has been formed, the first step in an RCA is to create a problem statement. This is not necessarily wrong, but often the ideas listed do not clearly contribute to the failure under investigation. Often, failure investigations begin with brainstorming possible causes and listing them in an Ishikawa diagram. RCA can progress more quickly and effectively by pairing an Ishikawa diagram with the scientific method in the form of the well-known plan-do-check-act (PDCA) cycle to empirically investigate the failure. Root cause analysis (RCA) is a way of identifying the underlying source of a process or product failure so that the right solution can be identified.
